在實(shí)際的LCD顯示面板制作過(guò)程中,工藝要求極為復(fù)雜,所用設(shè)備較多,環(huán)境要求嚴(yán)格。
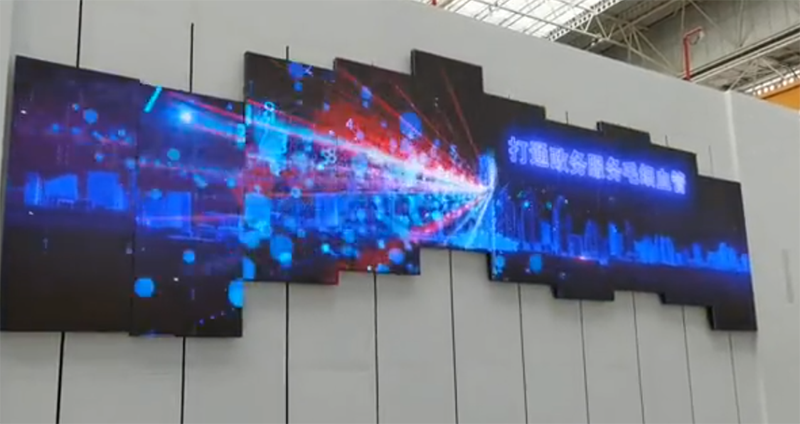
為此,需要提供一種
拼接屏及制作方法,解決拼接屏的顯示效果較差,拼接屏的拼接縫較明顯的問(wèn)題。
為實(shí)現(xiàn)上述目的,本實(shí)施例提供了一種拼接屏制作方法,包括如下步驟:
在基板的一面上制作薄膜晶體管和第一電極,所述第一電極位于所述薄膜晶體管的一側(cè);
制作平坦層,所述平坦層位于所述薄膜晶體管和所述第一電極上;
在平坦層上制作第一孔和第二孔,所述第一孔的孔底為薄膜晶體管的源極或者漏極,所述第二孔的孔底為第一電極;
制作第二電極和第三電極,所述第二電極通過(guò)所述第一孔連接薄膜晶體管的源極或者漏極,所述第三電極通過(guò)所述第二孔連接第一電極;
制作像素定義層,并在像素定義層上制作第三孔,所述第三孔的孔底為第二電極;
在第三孔中制作發(fā)光層,所述發(fā)光層連接所述第二電極,至此得到顯示子屏;
在像素定義層上制作第四孔,第四孔的底部為第二電極,將兩個(gè)顯示子屏的連接側(cè)壁通過(guò)導(dǎo)電銀漿拼接在一起,所述導(dǎo)電銀漿通過(guò)第四孔連接兩個(gè)顯示子屏上的第三電極,所述導(dǎo)電銀漿還位于兩個(gè)顯示子屏的連接側(cè)壁之間,每個(gè)顯示子屏中第三電極均位于所述發(fā)光層和所述連接側(cè)壁之間;
在基板的另一面上制作驅(qū)動(dòng)芯片,所述驅(qū)動(dòng)芯片連接所述導(dǎo)電銀漿。
進(jìn)一步地,在第三孔中制作發(fā)光層的具體步驟為:
采用錫膏將miniled的發(fā)光層的燈珠引腳和所述第二電極相連接。
進(jìn)一步地,還包括如下步驟:
在兩個(gè)顯示子屏的像素定義層上制作有機(jī)封裝層,所述有機(jī)封裝層覆蓋像素定義層和第四孔中的導(dǎo)電銀漿。
進(jìn)一步地,在基板的一面上制作薄膜晶體管和第一電極后,在制作平坦層前,還包括如下步驟:
制作遮光層,所述遮光層位于薄膜晶體管和平坦層之間,所述遮光層用于阻擋光線照射薄膜晶體管中的有源層。
進(jìn)一步地,所述薄膜晶體管為底柵結(jié)構(gòu),所述第一電極和源極同層設(shè)置。
本實(shí)施例還提供一種拼接屏,包括導(dǎo)電銀漿、驅(qū)動(dòng)芯片和顯示子屏;
所述顯示子屏包括薄膜晶體管、第一電極、平坦層、第二電極、第三電極、像素定義層和發(fā)光層;
所述薄膜晶體管和所述第一電極均設(shè)置在基板的一面上,所述第一電極位于所述薄膜晶體管的一側(cè);
所述平坦層設(shè)置在所述薄膜晶體管和所述第一電極上;
所述第二電極和所述第三電極均設(shè)置在所述平坦層上,所述第二電極通過(guò)平坦層上的第一孔連接薄膜晶體管的源極或者漏極,所述第三電極通過(guò)平坦層上的第二孔連接第一電極;
所述像素定義層設(shè)置在所述平坦層、所述第二電極和所述第三電極上;
所述發(fā)光層設(shè)置在像素定義層的第三孔中,所述發(fā)光層連接所述第二電極;
兩個(gè)的顯示子屏的連接側(cè)壁通過(guò)所述導(dǎo)電銀漿相拼接在一起,所述導(dǎo)電銀漿還通過(guò)像素定義層上的第四孔連接每個(gè)顯示子屏中的第三電極,其中每個(gè)顯示子屏中第三電極均位于所述發(fā)光層和所述連接側(cè)壁之間;
所述驅(qū)動(dòng)芯片設(shè)置在基板的另一面上,所述驅(qū)動(dòng)芯片連接所述導(dǎo)電銀漿。
進(jìn)一步地,所述發(fā)光層為miniled的發(fā)光層,miniled的發(fā)光層的燈珠引腳通過(guò)錫膏和所述第二電極相連接。
進(jìn)一步地,所述拼接屏還包括有機(jī)封裝層,所述有機(jī)封裝層不僅覆蓋每個(gè)顯示子屏中的像素定義層,還覆蓋第四孔中的導(dǎo)電銀漿。
進(jìn)一步地,所述顯示子屏還包括遮光層,所述遮光層位于薄膜晶體管和平坦層之間,所述遮光層用于阻擋光線照射薄膜晶體管中的有源層。
進(jìn)一步地,所述薄膜晶體管為底柵結(jié)構(gòu),所述第一電極和源極同層設(shè)置。
區(qū)別于現(xiàn)有技術(shù),上述技術(shù)方案通過(guò)導(dǎo)電銀漿來(lái)實(shí)現(xiàn)兩屏幕的無(wú)縫拼接,導(dǎo)電銀漿具備優(yōu)異的印刷性、耐水性、硬度、附著力、撓曲性及耐候性、導(dǎo)電性能,使得拼接屏上拼接縫較細(xì),不易給人一種突兀的感覺(jué)。同時(shí)上述技術(shù)方案還避免拼接屏上拼接縫的若干條暗區(qū),提高拼接屏的顯示質(zhì)量,提高產(chǎn)品的競(jìng)爭(zhēng)力。